Specialized for High-Speed Production

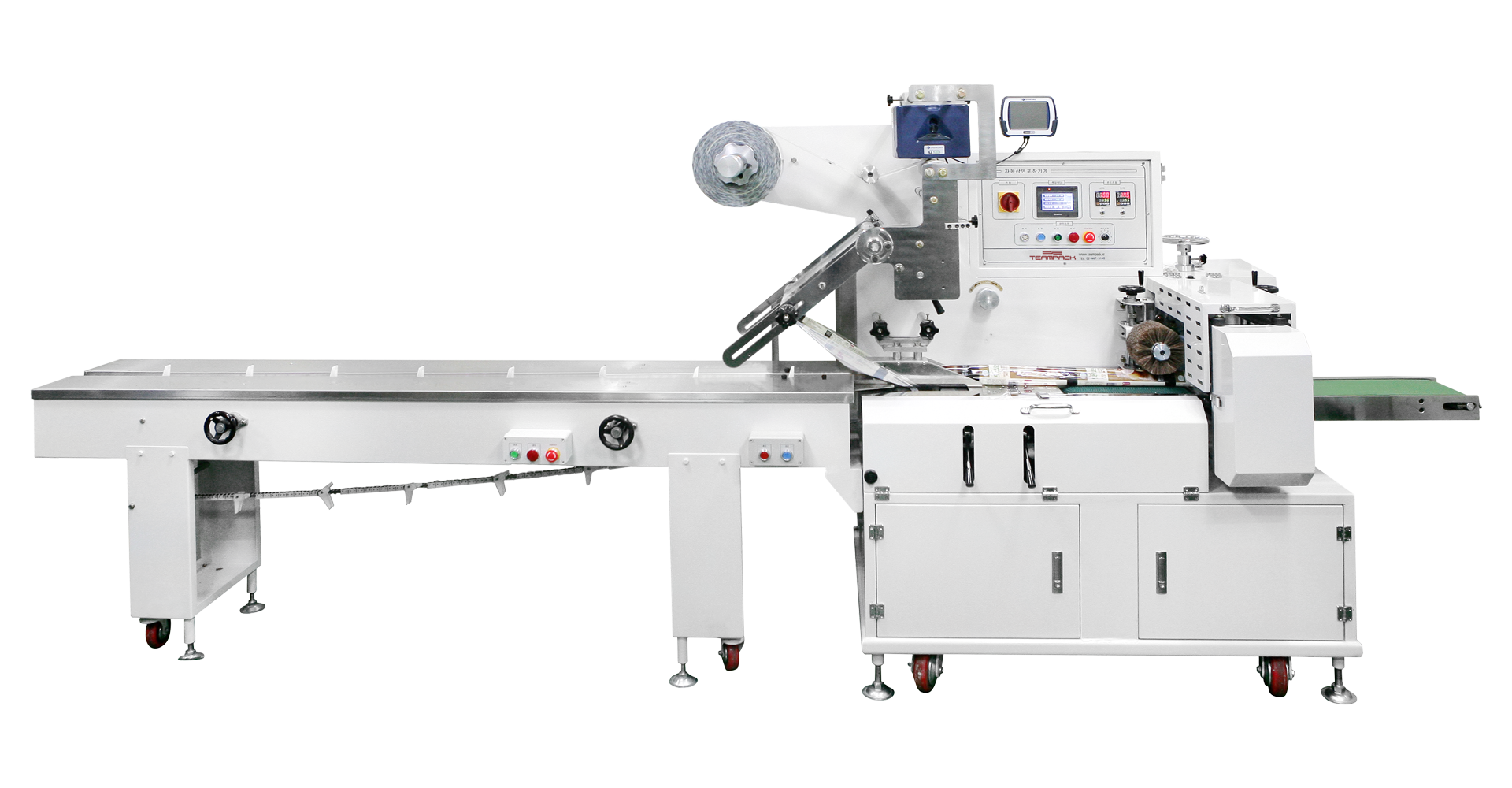
TPRA-101D
Top-Feed Pillow Packaging Machine (Rotary Type Cutter)
The TEAMPACK top-feed pillow packaging machine with rotary type cutter is designed for high-volume production in the bakery, food, pharmaceutical, and household goods industries. Using a bottom-sealing method where the film feeds from above and forms a back seal beneath the product, it is ideal for tray-packed, baked, or container-type items with distinguishable top and bottom sides. Among TEAMPACK’s pillow pack models, it delivers the highest packaging speed.
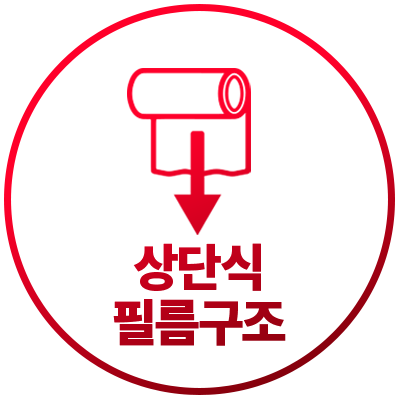
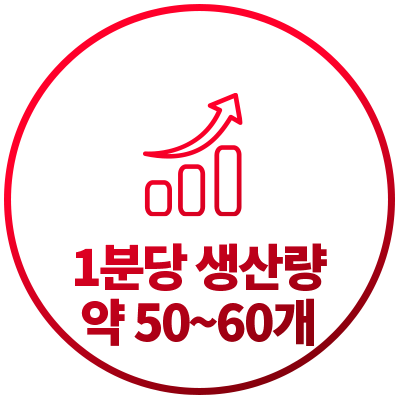
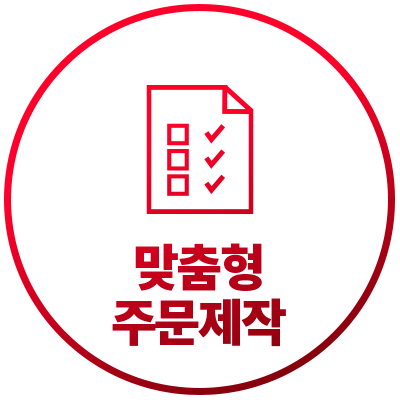
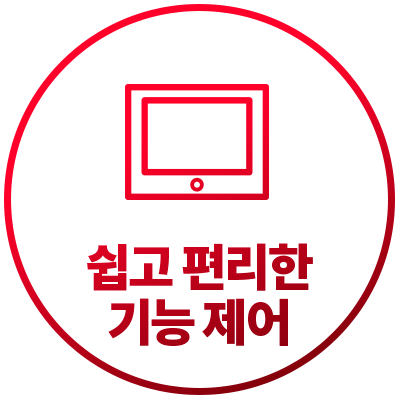
Optimized for high-volume production
Rotary-Type Cutting Line
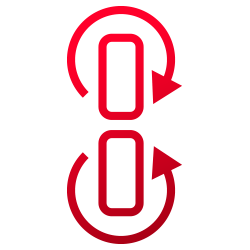
Rotary Type Mechanism
– Cutter rotates in place for continuous film cutting
– Highest packaging speed among all models
– Dedicated for short-height, compact-length products
– Specialized for packaging tray-packed food items
– Precision digital temperature controller
– Custom-built feeding lines tailored to client requirements
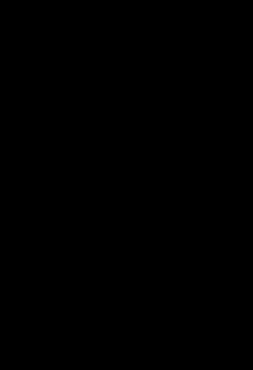
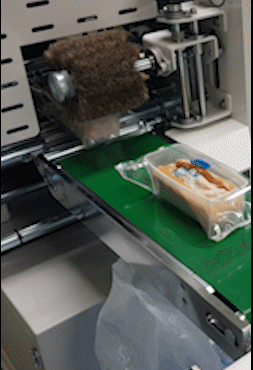
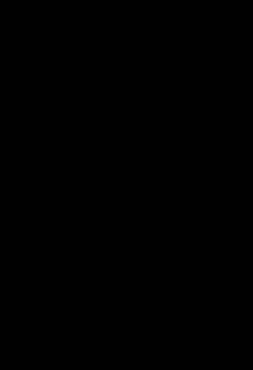
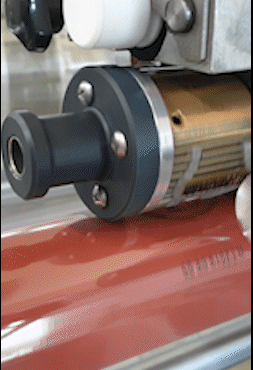
Everything from startup to machine control
All-in-One Touchscreen Control System
One touch is all it takes to control machine.
The TEAMPACK pillow packaging machine integrates advanced hardware and software for real-time precision control, converting film measurements and sensor signals into actionable data. Digital inputs from each line are processed through correction algorithms and feedback loops, enabling accurate monitoring and rapid control of film length, sealing, and cutting—regardless of production conditions.
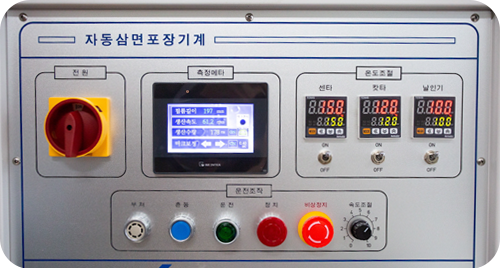
Intuitive Control Box
The control box is designed for centralized, user-friendly operation. Featuring a large touchscreen, temperature control panel, and action switches, the interface allows operators to monitor all processes in real time with clarity and ease. The power switch has a clearly defined On/Off display with indicator lights, ensuring straightforward and safe operation.
– Operates on 220V single-phase power
– Maximum power consumption: approximately 4kW
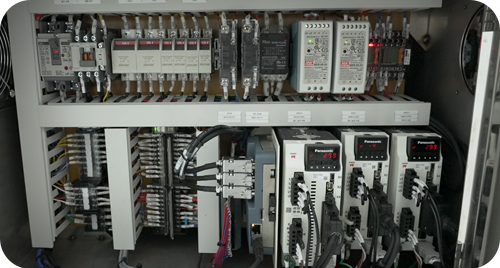
Powered by LS Industrial Systems PLC
The TEAMPACK pillow packaging machine offers fully customizable control of all machine operations to suit on-site production requirements. The PLC system enables seamless integration with peripheral devices and interlocks. Digital signals from each sensor and operational unit are processed in real time, allowing the high-performance CPU and central controller to execute independent commands and monitor all machine functions with ultra-fast, high-precision responsiveness.
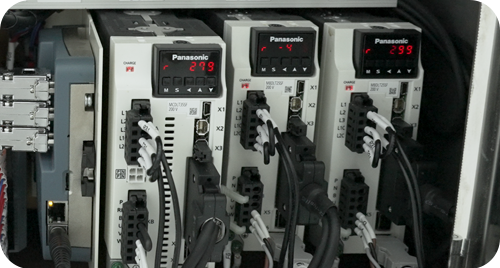
Panasonic Servo Driver
– Control Modes: Position, speed, torque, and full-closed loop control
– Power Supply: Supports 200V single- and three-phase input
– Input Types: Analog and pulse train compatible
– Communication: Modbus via RS485/RS232 for system integration
– Bandwidth: 3.2 kHz for fast, precise response
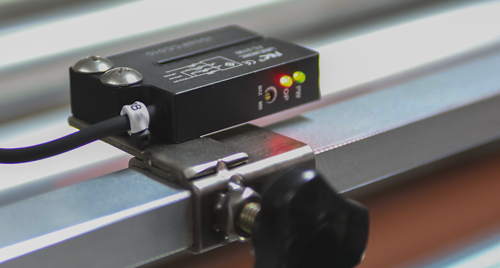
Electronic I-Mark Positioning
Conventional machines require manual adjustment of three axes to align the I-Mark and product position, often resulting in time-consuming setup and excess film waste. The TPBMA-SS101D3SV allows operators to simply input the desired value—automatically adjusting the position for immediate and precise cutting, with no manual intervention or film loss.

DOMINO Thermal Transfer Printer
– 7” touchscreen for easy message editing
– 300 dpi high-resolution printing
– Speed: up to 600 mm/s (intermittent), 750 mm/s (continuous)
– Fully electric — no compressed air required
*This unit is optional.
*Specifications may vary depending on production conditions.
For precise placement
Top-Feed is The Answer.
Under-product fin seal.
With the film positioned on top, operators can adjust it easily without bending. The open-frame design enables direct visual alignment of the I-Mark during film movement. A secure film bracket and fine-tuning handle allow quick and simple film adjustments even during production.
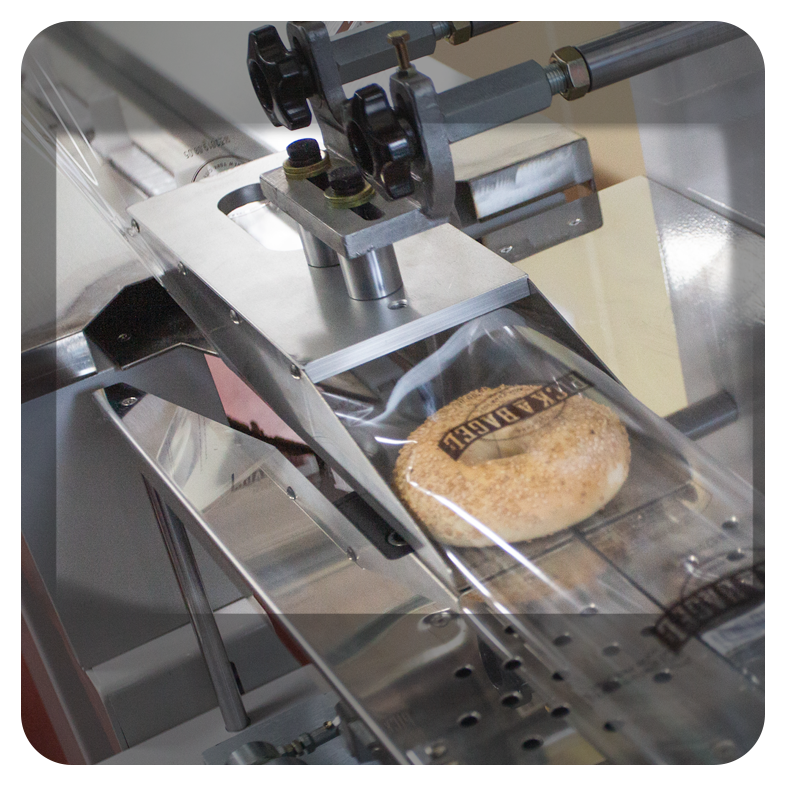
Product Infeed
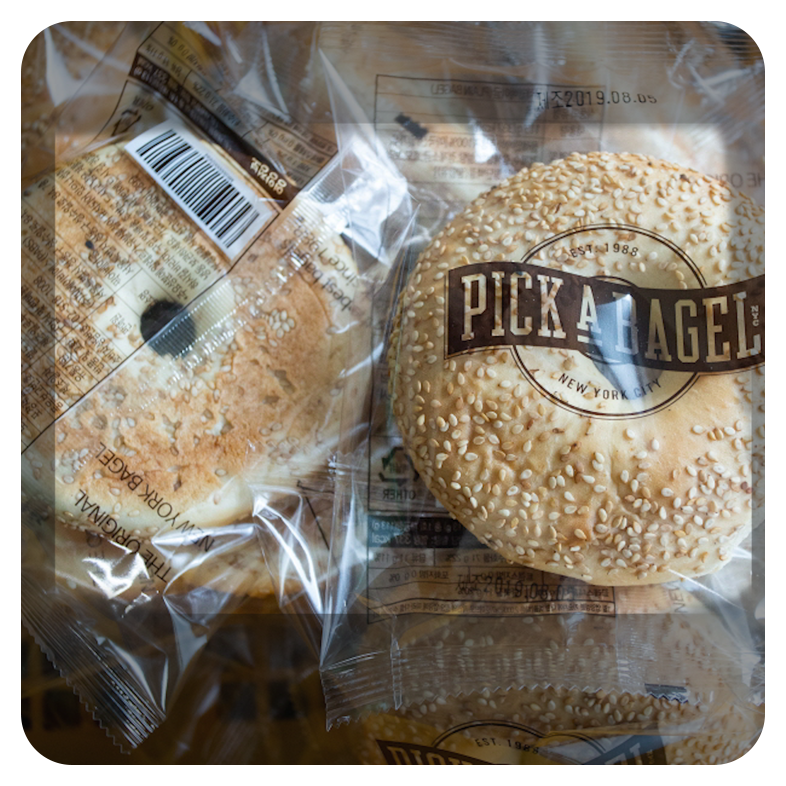
Finished Package
Hygienic & customizable
Custom-Built Feed Conveyor.
Safe and hygienic product feeding conveyor.
The feed conveyor, responsible for transporting products to the packaging section, uses POE (Polyolefin Elastomer) attachments where items are placed, while the frame is constructed from hygienic stainless steel 304. TEAMPACK offers fully customizable conveyor configurations to suit different product shapes and packaging needs.
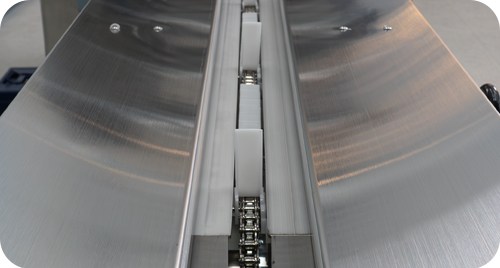
POE Material
POE (Polyolefin Elastomer) is a high-performance thermoplastic known for its dimensional stability and excellent resistance to deformation. As an engineering plastic, it offers strong chemical resistance and corrosion protection across various environments. Its outstanding insulating properties also make it resistant to static electricity, creating a stable and hygienic environment for safely transferring food, pharmaceutical, and consumer goods through the feed conveyor to the packaging section.

Sub Controller
The feeder conveyor is equipped with run, stop, and emergency stop switches, allowing operators to control the main pillow packaging machine directly from the conveyor. This enables safe and efficient operation without having to move to the main control panel, even while feeding products into the system.
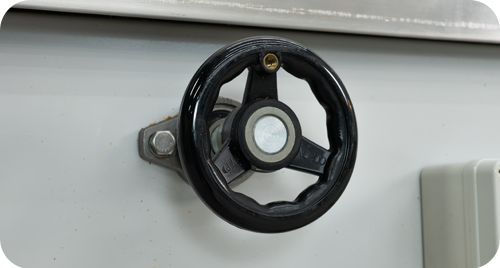
Adjustment Handle
The feeder conveyor is equipped with a side-mounted adjustment handle that allows operators to widen or narrow the side guides. This design enables easy packaging of products in various sizes.
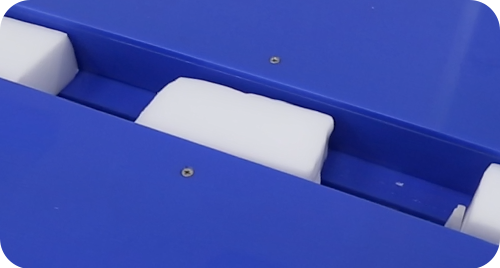
PE Material
Polyethylene (PE) is a thermoplastic resin with high impact strength at low temperatures. Its low moisture absorption, excellent chemical resistance, and corrosion resistance make it ideal for dry ice packaging. TEAMPACK offers custom-built conveyors using PE material specifically designed for dry ice handling environments.
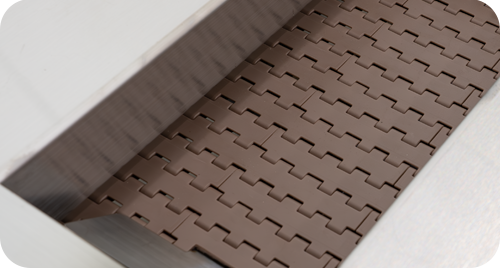
Fresh Food Packaging
TEAMPACK offers conveyor systems specialized for packaging fresh products such as vegetables, fruits, baked goods, and pharmaceuticals. These systems prioritize temperature, humidity, and hygiene control, using carefully selected materials to meet food safety standards. Unlike conventional industrial conveyors, they are engineered with features that prevent contamination and ensure compliance with strict sanitary requirements.
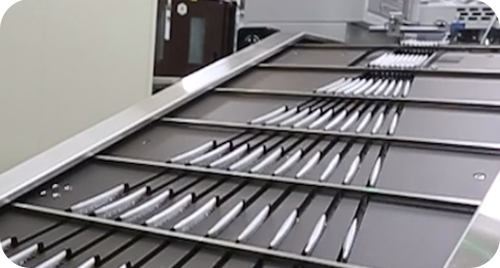
Tailored Engineering
TEAMPACK offers both belt-type and rod-type feeder conveyors, custom-built to meet the unique needs of each production environment. By integrating various transfer systems, we optimize packaging lines for specific industries and product types. Through detailed customized design, TEAMPACK ensures seamless compatibility with existing automation equipment and machinery—delivering solutions engineered exclusively for each customer.
Independent temperature control
for Sealing and Cutting!
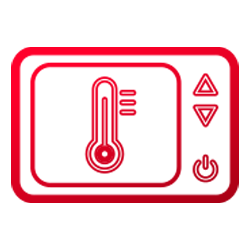
Digital temperature controller
Main control box
(temperature control section)
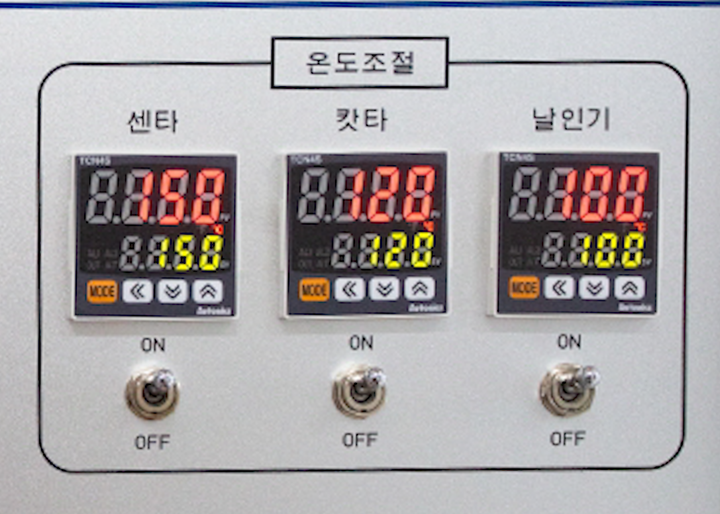
Center sealer
(sealer temperature setting)
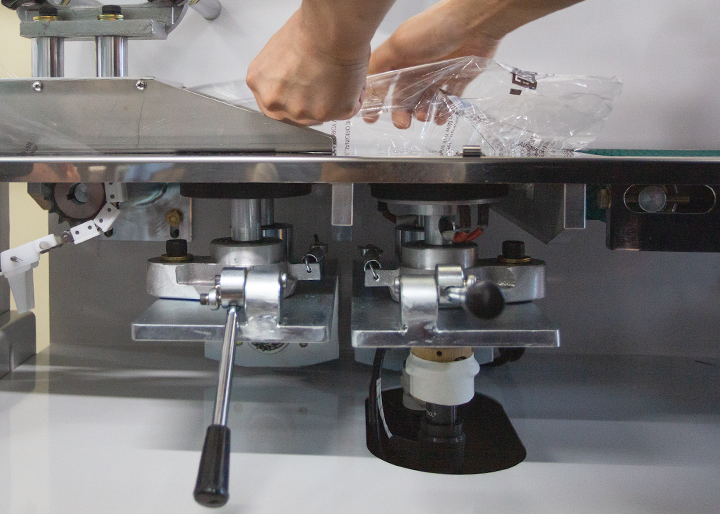
Cutter sealer
(cutter temperature setting)
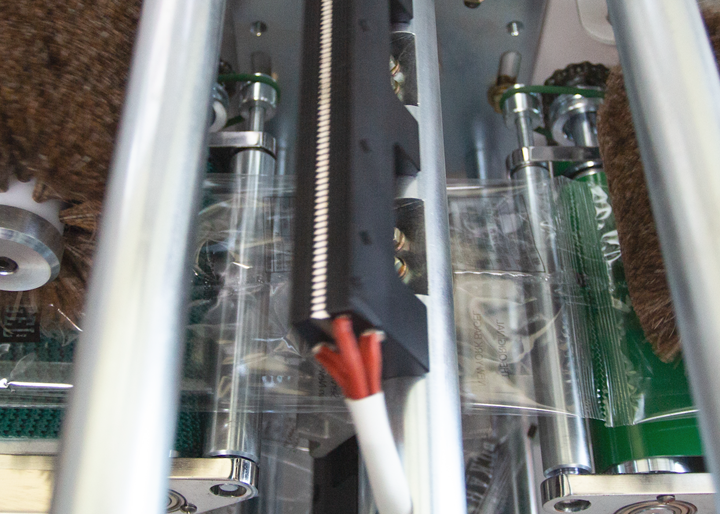
Operator protection comes first!
Safety-First Design.
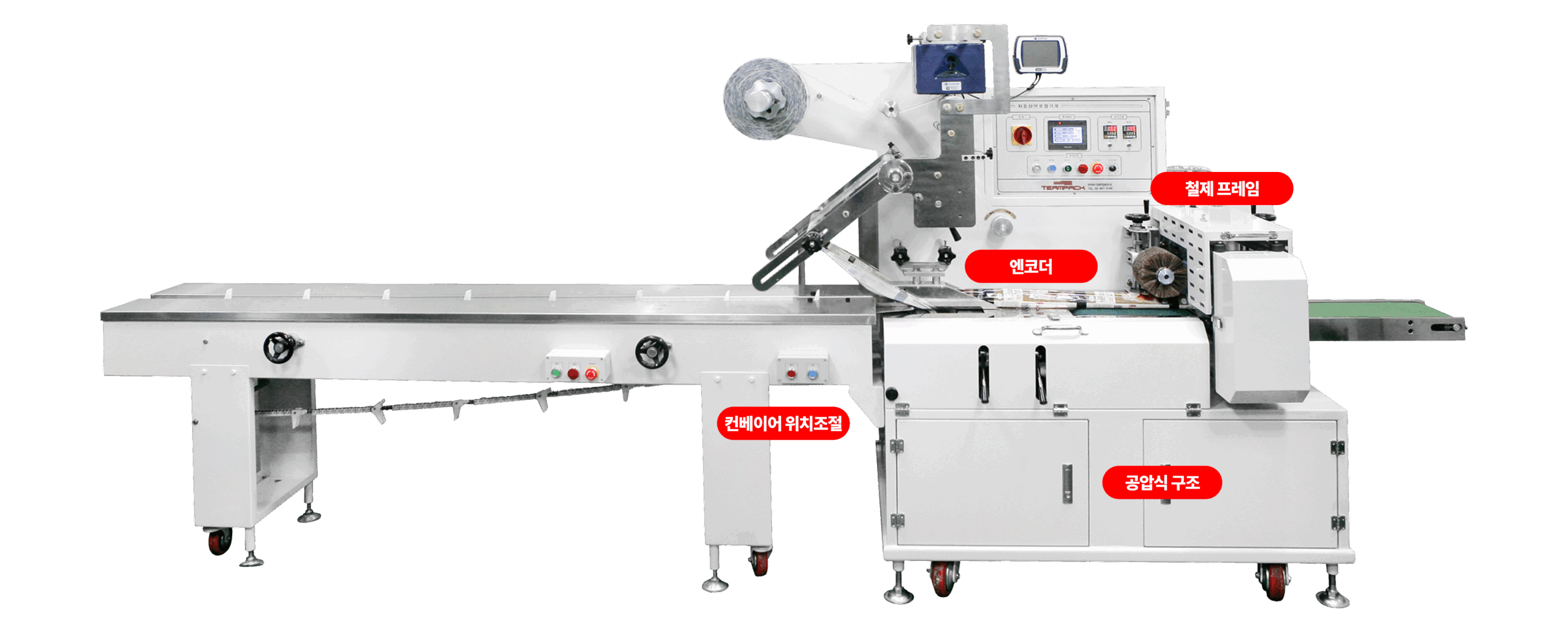
Adjustment Button
Simple forward/reverse
conveyor buttons
Encoder
Dial-type
film length control
Safety Frame
Openable steel safety guard for operator protection
PNE System
Automatic separation of sealing rollers & cylinder motion
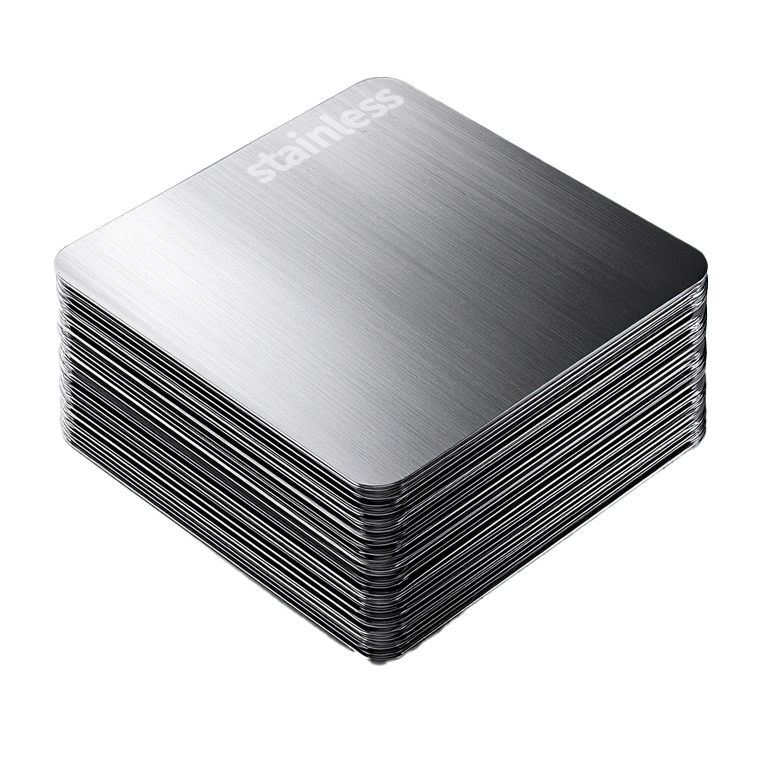
SUS-304
Stainless Steel 304 Construction
Cutter Types
① Rotary Cutter: A continuously rotating blade system ideal for high-speed packaging of small, uniform products. (Recommended for: snacks, chocolates, face masks, medical products)
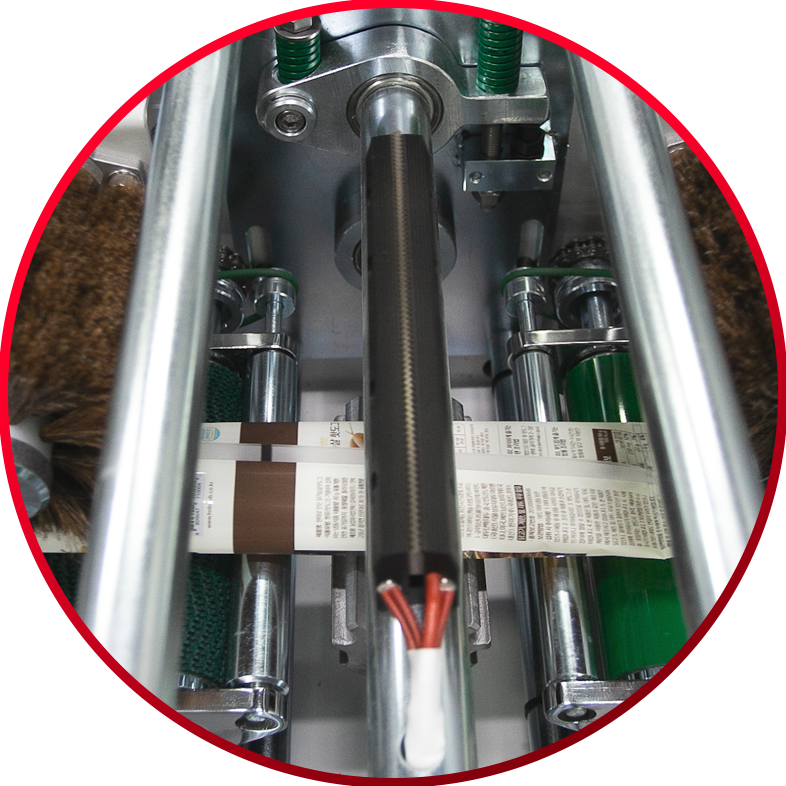
② Cylinder Cutter: A vertical cutting mechanism that delivers exceptionally tight and precise seals between the product and film. (Recommended for: frozen foods, general consumer goods)
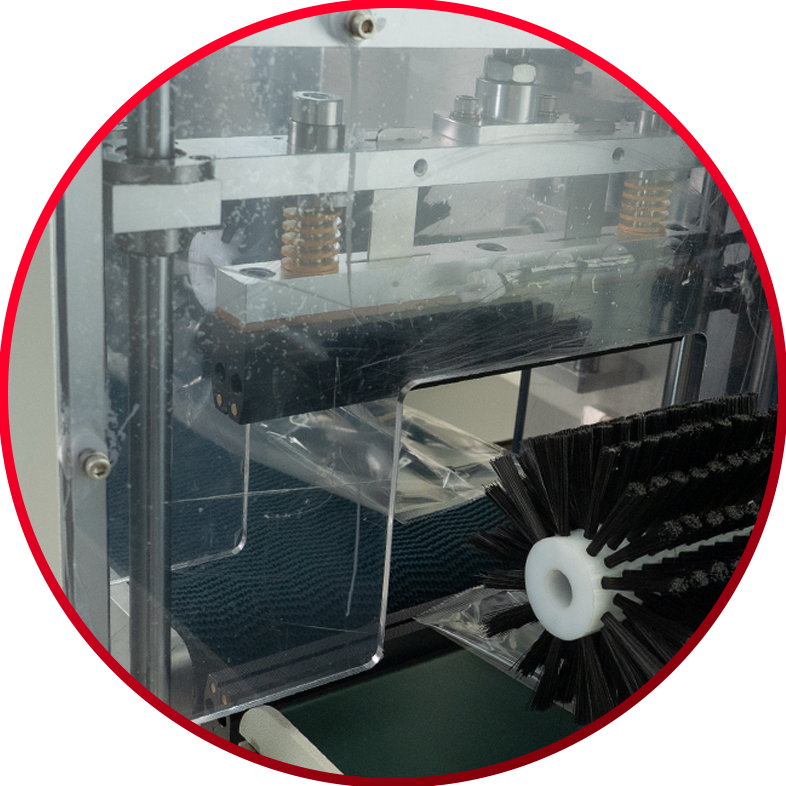
③ Box Motion Cutter: Ideal for tall or irregular-sized products, offering stable speed and superior seal quality. (Recommended for: bread, books, panels)
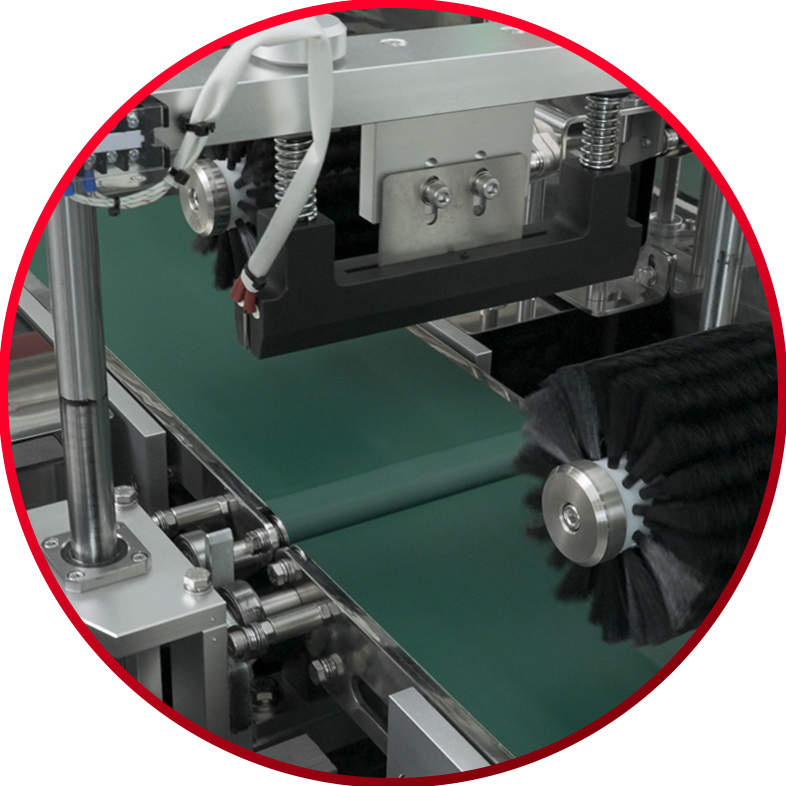
Explore other models.
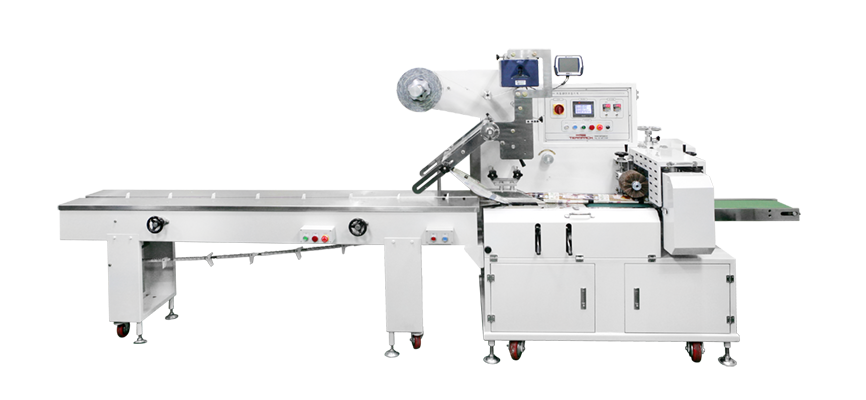
TPRA-101D
Top-Feed PPM – Rotary
Packaging capacity: approx. 50–60 packs/min (high-speed production model)
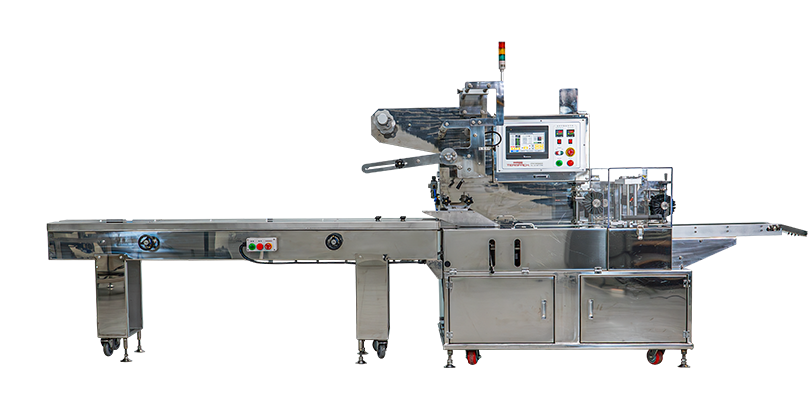
TPBMA-SS101D3SV
삼면포장기 상단식 박스모션
3축서보 스테인리스 타입
분당 포장 캐파 : 약 30~40개 (하이-엔드 모델)
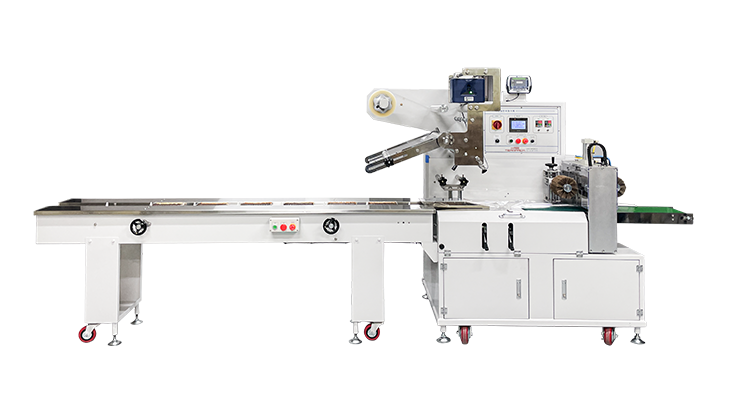
TPRA-101D
삼면포장기 상단식 로타리 타입
분당 포장 캐파 : 약 50~60개 (고속생산 전용모델)
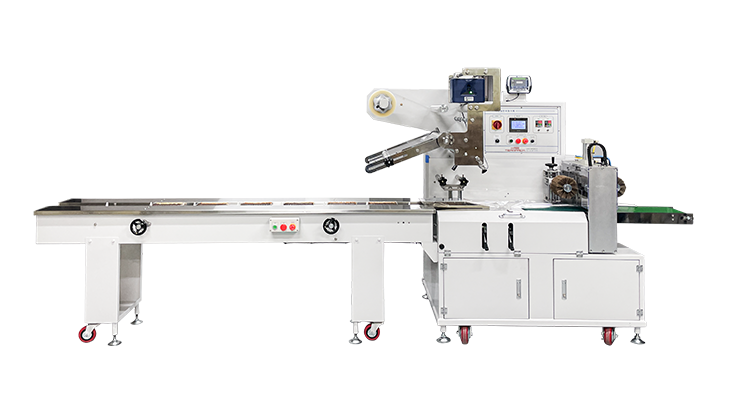
TPRA-101D
삼면포장기 상단식 로타리 타입
분당 포장 캐파 : 약 50~60개 (고속생산 전용모델)
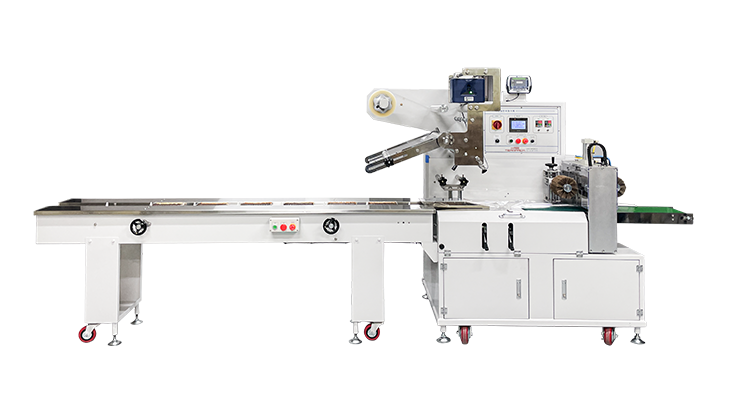
TPRA-101D
삼면포장기 상단식 로타리 타입
분당 포장 캐파 : 약 50~60개 (고속생산 전용모델)
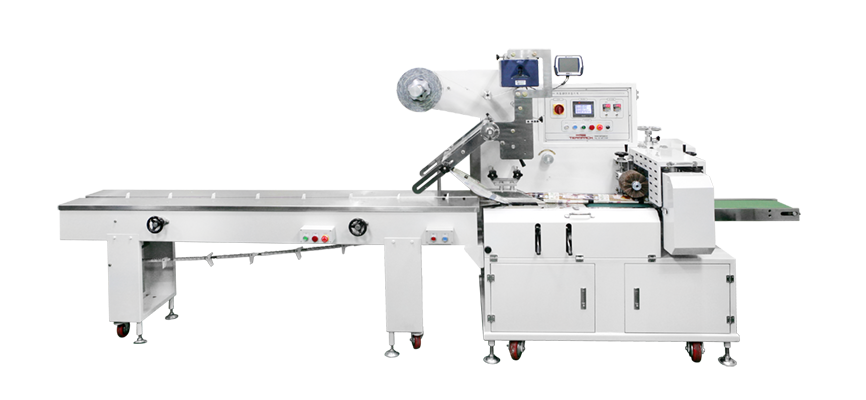
TPRA-101D
Bottom-Feed PPM – Rotary
Packaging capacity: approx. 50–60 packs/min (high-speed production model)
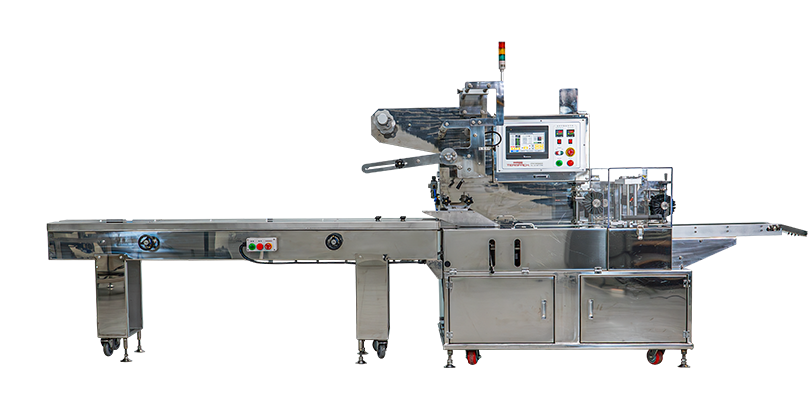
TPBMA-SS101D3SV
삼면포장기 상단식 박스모션
3축서보 스테인리스 타입
분당 포장 캐파 : 약 30~40개 (하이-엔드 모델)
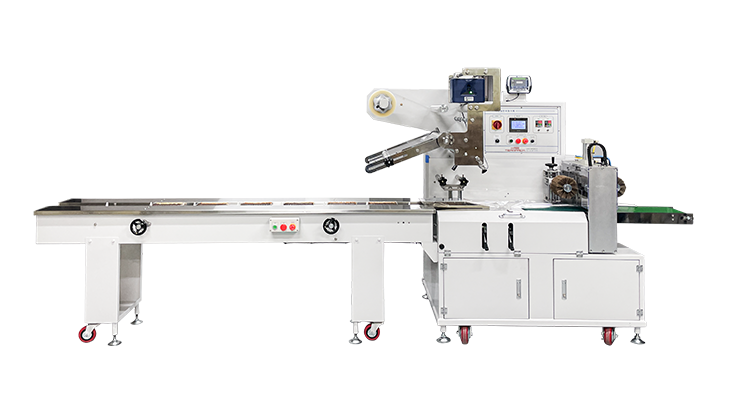
TPRA-101D
삼면포장기 상단식 로타리 타입
분당 포장 캐파 : 약 50~60개 (고속생산 전용모델)
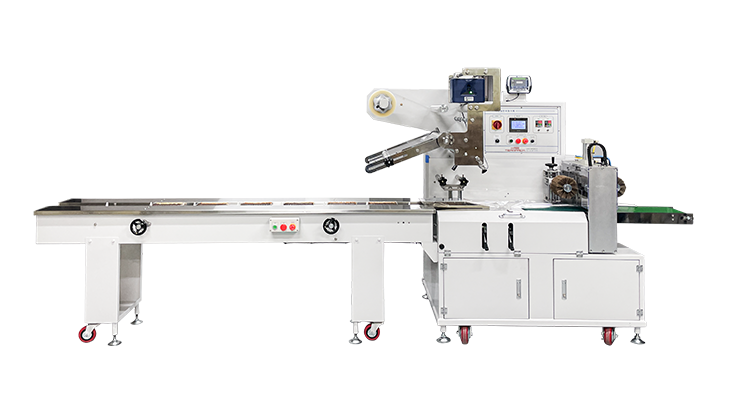
TPRA-101D
삼면포장기 상단식 로타리 타입
분당 포장 캐파 : 약 50~60개 (고속생산 전용모델)
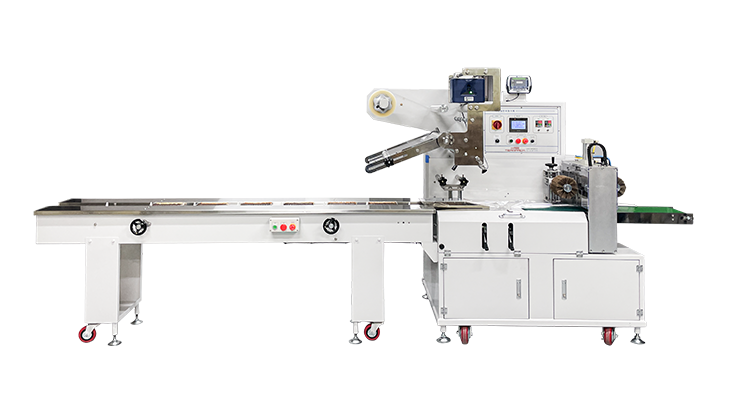
TPRA-101D
삼면포장기 상단식 로타리 타입
분당 포장 캐파 : 약 50~60개 (고속생산 전용모델)
Technical Specifications
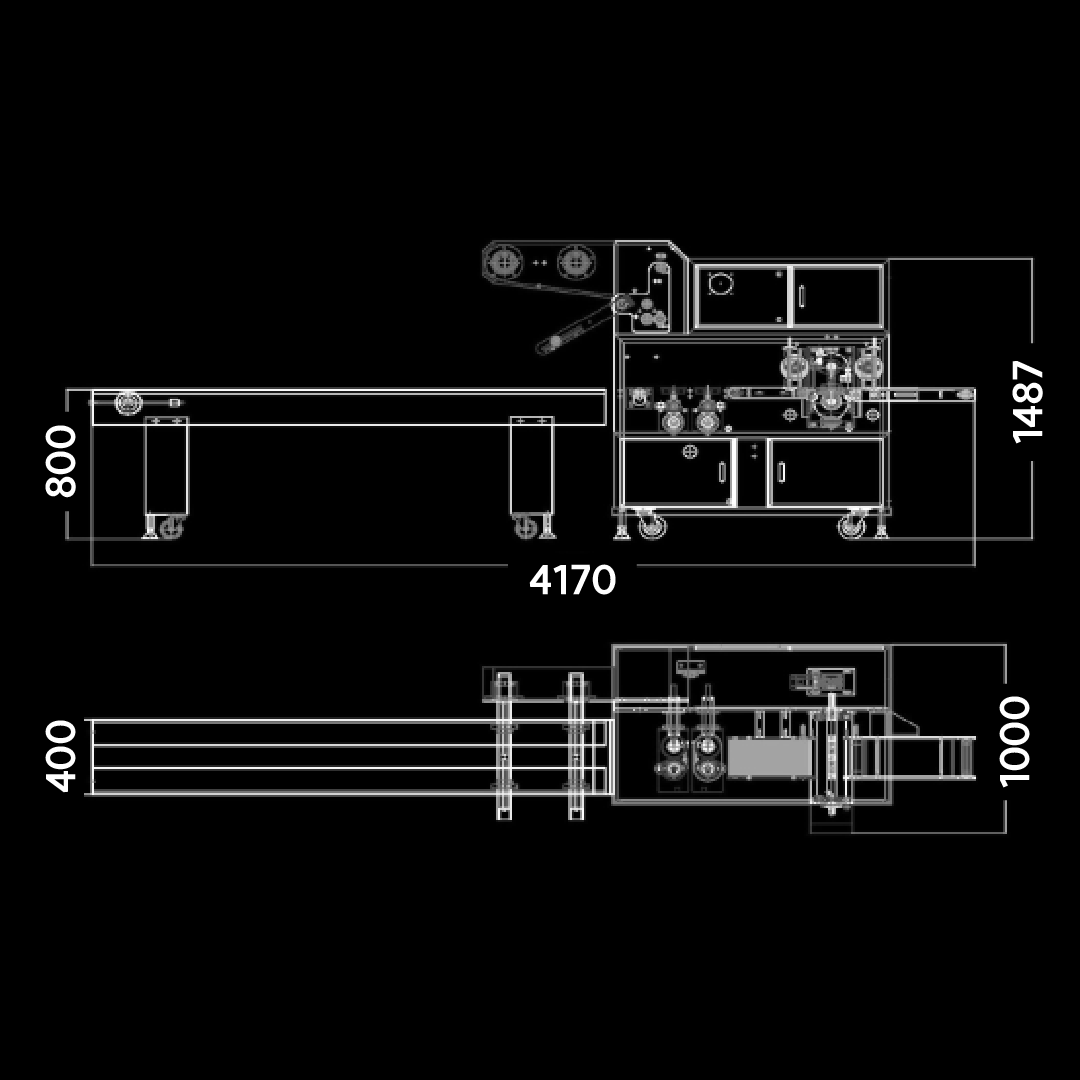
TPRA-101D
Power Supply
220V, Single Phase, 60Hz
Maximum Power Consumption: Approx. 2.6 kW
Dimensions
L: 4,200 mm
W: 1,050 mm
H: 1,630 mm